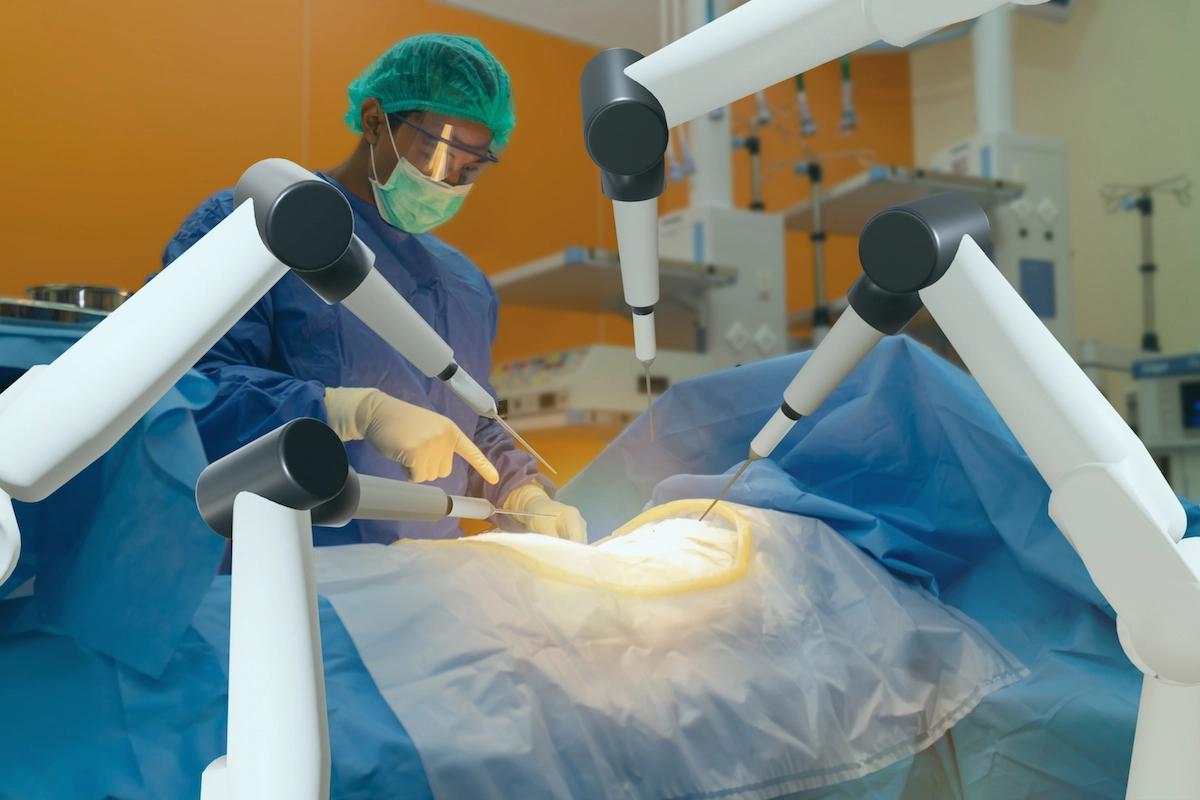
客户情况
一家外科机器人公司与Aptyx合作,分两个阶段为下一代机器人手术系统开发了26个组件。原来的齿轮装配结构是一个黄铜齿轮,带有不锈钢轴和包胶的两部分齿轮片。将轴压入轮片属于劳动密集型手工作业,成本高,耗时长,并产生质量隐患。原来的轮片有一个机械轮毂,是手工上料,热塑性聚氨酯(TPU)包胶成型,需要手动修剪到大小。
客户的目标是在降低成本的同时提高组件质量并确保一致性和及时的交付。他们选择与Aptyx合作,因为我们在制造精密齿轮和复杂成型专业知识方面拥有70年的历史,特别是在双射成型方面。
Aptyx 方案
在这个项目中,Aptyx利用了其在聚合物材料、齿轮、内部模具设计和制造方面的专业知识,以及注塑成型,包括镶嵌和二次成型,以及由专业的模具工程师进行工艺开发并得到了强有力的项目管理和质量工程的进一步支持。
Aptyx团队利用其注塑成型可制造性(dfinm)原则的深度设计来修改客户的原始设计,以适应关键齿轮应用的注塑成型塑料部件,包括不锈钢轴的包胶成型和轮片的二次成型。
材料选择是取得精密齿轮高性能的关键。材料的变化需要彻底了解应用和性能要求,以及聚合物齿轮的特点。该团队考虑的一些因素包括:
- 齿轮的尺寸、形状和配置以及关键的齿轮啮合界面
- 热膨胀:轴向和径向尺寸在不同温度下如何变化
- 齿轮的齿形确保运转平稳,啮合良好
- 消除尖角,造成压力,导致裂缝或断裂
- 不锈钢轴的临界过模界面和扭矩要求
在第一阶段,改进后的轮片设计采用了一射聚碳酸酯(PC)轮毂和二射聚氨酯涂层。对于该组件,Aptyx团队调整了他们的双注射成型机器,并开发了一种工艺,首先注射PC轮片,然后再注射聚碳酸酯轮毂,这取代了人工二次处理操作,节省了人工费,并消除了内轮片需机械加工,并且省去了检查、搬运、过度成型二次修整操作流程,从而节省了80%以上的成本。
复杂的齿轮和轮片采用注塑成型,内径上有严格的公差,用于轴承过渡配合,外径压配合用于齿轮轮毂上的轮片。齿轮由乙缩醛聚合物模制而成,这种聚合物非常适合需要高承载能力、抗变形性、润滑性以及平稳、安静运行的应用。
在第二阶段,该团队获得了公差最严格的复杂组件项目,其中包括对几个大型模制组件的额外成本节约改进。许多当前的生产零件需要昂贵的二次加工操作来满足公差和关键功能要求。这些较大的零件需要由Aptyx和第三方合作伙伴完成全面的Moldflow®分析。此外,这些零件需要大量复杂的模具设计,其中包括多个滑动操作和刀片区域以及计划中的模具刀片特征,以满足严格的公差要求。最后,为了确保满足关键公差,ptyx利用了他们内部的计量实验室,包括VMM和基于模型的CMM,以及第三方CT扫描检查的专业知识。
成果
从黄铜齿轮到聚合物齿轮的变化以及双射注塑装配带来了大约80%的成本节约。此外,由于减少了加工和分步装配操作,新的制造工艺缩短了生产时间,更好地控制了产品质量。
“Aptyx团队在将黄铜齿轮转化为塑料方面做得非常出色,”客户的首席工程师说。“由于设计上的挑战,在齿轮和包胶成型方面的深厚专业知识至关重要。该团队还将一个昂贵的、劳动密集型的、存在质量问题的部件转换为双注射成型,这大大降低了成本,提高了质量,并轻松满足了生产需求。”
“Aptyx为我们带来了成功,因为它有非常好的项目管理和良好的技术专长,”客户说。“他们是项目成功的关键,包括一个大型的、经验丰富的跨职能团队和DFM的实力。这个团队非常彻底,审查并完成了许多许多模具师忽略的细节。他们的质量文件也非常彻底和完整.”